THE RECOMPOSED PROJECT
(aRbrE COMPOSitE)
How did the RECOMPOSE project come about?
The RECOMPOSE project has its origins in the scientific and industrial prospects observed during the STEADIEST project (partially funded by CleanSky).
Our intention to improve the maturity of the technologies developed – on new application cases – was encouraged by CORAC, in line with its helicopter roadmap. NEXTEAM, together with Airbus Helicopters, which provided a case study and support, then applied for the 2020 recovery plan before being selected to lead this project in collaboration with two partners.
NEXTEAM is once again investing in RECOMPOSE, with the ambition of advancing technology in aeronautics, to affirm its position as a dynamic assemblies supplier.
What is the Recompose project ?
This project is funded by the European Union NextGeneration EU, the DGAC and is supported by CORAC. It aims to increase the competitiveness of helicopters while reducing their CO2 emissions.
The partners are proposing modernised power transmission solutions to reduce product weight, production costs and operating costs by at least 25%. In addition, a number of scientific challenges, such as the digital twin, have been defined and will be studied as part of this project to shorten the development times inherent in the aerospace industry.
Following on from the STEADIEST project, NEXTEAM will draw on :
- Its architects and calculators to define and size the product
- Its engineers and testing facilities to demonstrate the product’s performance experimentally
- Its patents, production facilities and accreditations to manufacture and deliver a drive train for flight testing.
The main challenges are to
- Rationalise the architecture of a helicopter’s rear power transmission to achieve substantial weight and cost savings.
- Demonstrate and produce a complete and representative rear power transmission demonstrator, with a view to integration and testing on a helicopter.
- Draw up a clear assessment of the technological opportunities that can be transposed to other applications in the aeronautics and space sector.
The consortium: 3 partners
NEXTEAM is coordinating the project and will be responsible for the general definition of the composite drive train, the processes and the linking components. The project involves 10 employees in the design and production departments.
CT Ingénierie will participate in the development of the production processes and the Structural Health Monitoring systems.
AMVALOR will carry out vibration studies and experiments on the dynamic assemblies, as well as impact studies on the digital twin.
Follow the progress of the project as it unfolds
Our partners
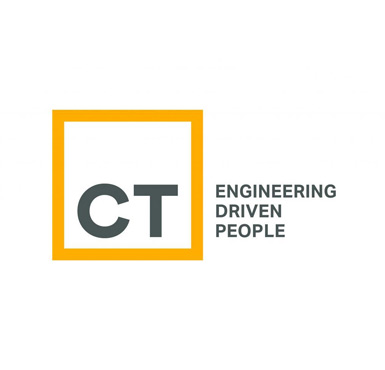
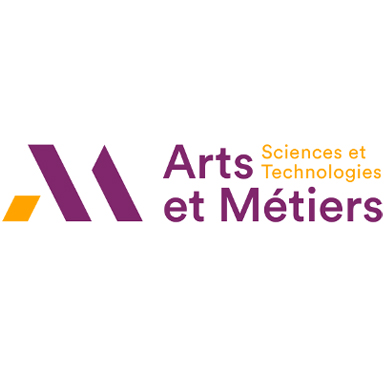
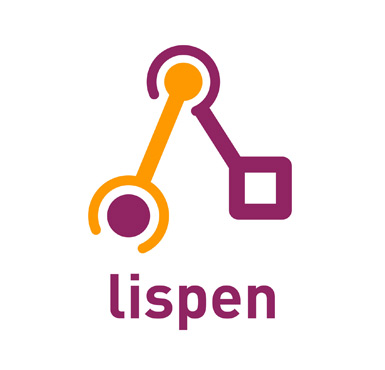
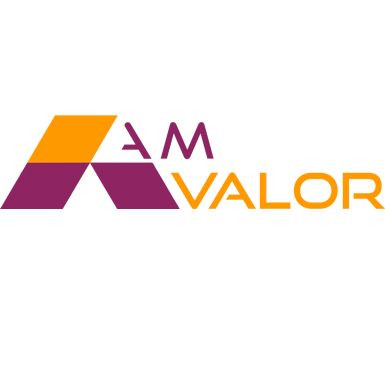